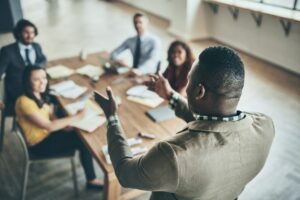
Empowering Your People Isn’t Enough | DConsulted
Learn why empowering employees alone doesn’t guarantee success. Discover how strategic alignment and leadership support drive real results.
The concept of functional safety began to take shape in the mid-20th century, first established within the broader disciplines of safety and reliability engineering. As industries such as aerospace and automotive adopted more sophisticated technologies, the need to mitigate risks and ensure the reliability of complex systems grew rapidly in response.
Consequently, Fault Tolerant Time Interval (FTTI) has gained prominence and formal recognition in engineering practices and safety standards such as ISO 26262. This is underscored by the automotive industry’s increasing reliance on sophisticated electronic control systems such as advanced driver assistance systems (ADAS) and autonomous vehicles, which require stricter timing requirements under fault conditions.
FTTI is a central concept in safety-related systems. It refers to the maximum duration that can elapse from the moment a fault occurs within the system to the point where failure to perform the intended safety function could lead to an unsafe condition. In simpler terms, FTTI is the interval within which the system must detect and address a fault to prevent any potential hazards.
This time interval is comprised of three key components:
If the system fails to detect or address a fault within the FTTI, its ability to perform crucial safety functions — such as detecting a pedestrian, deploying an airbag, or sensing a loss of traction — may be compromised. This failure to manage the fault within the interval can lead to the system reaching an unsafe state where it can no longer ensure the safety of the controlled process or environment.
The ISO26262 standard places a strong emphasis on ensuring that this time interval is accounted for in the design to guarantee that any faults do not lead to hazardous outcomes before they can be managed. The standard also requires that the occurrence, detection, and reaction times be validated and verified to confirm that they function as intended under various conditions.
The importance of FTTI goes beyond the simple summation of fault detection and reaction times. It includes other critical elements that enable robust safety designs and the system’s ability to handle transient faults such as electronic throttle control systems causing unintended acceleration or fuel injection malfunctions affecting engine performance. These are detected promptly to activate safety redundancies and prevent potential hazards.
Another key aspect of FTTI in automotive safety design is its consideration of the periods involved in managing faults and hazards. This is where the concepts of latency, tolerances, and safety margins come to the forefront.
Latency Before Hazard considers the time frame in which a system can operate in a degraded state before an immediate hazard occurs. This latency offers a vital window for intervention and corrective action, allowing the system to address potential risks before they escalate into hazardous situations.
For example, when a potential collision is detected in an autonomous braking system, the system processes the information, decides on a response, and executes braking. The FTTI includes the time to detect and react to a fault, plus the period during which the vehicle can operate safely before a hazard occurs. This latency allows the system to alert the driver, activate backups, or safely stop the vehicle.
System Tolerances and Safety Margins incorporate additional safety margins and tolerances into the safety system design. These margins act as buffers against uncertainties and variations encountered in real-world conditions, ensuring the system’s resilience and reliability beyond idealized scenarios.
For example, in an Electronic Stability Control (ESC) system, tolerances and safety margins are essential for maintaining stability and preventing skidding. Real-world factors such as road conditions, tire wear, and weather can impact ESC performance. FTTI incorporates safety margins to accommodate these variables. In this instance, the ESC detects loss of traction and adjusts brake pressure on specific wheels to maintain stability. Tolerances account for variations in sensors and actuators, ensuring the ESC can correct and prevent skidding even when components are not operating at peak efficiency.
The Fault Tolerant Time Interval (FTTI) equation is not a specific formula but rather a conceptual representation within the framework of ISO 26262 standards. FTTI is the maximum time span in which a fault can be present in the system before it leads to a hazardous event. It is calculated based on the combination of the time required to detect a fault and the time required to react to that fault.
FTTI > {Fault Detection Time} + {Fault Reaction Time}
Basically, the equation specifies that to maintain safety, the system must be designed such that the combined time for detecting and reacting to faults is always less than the Fault-Tolerant Time Interval. If this condition is met, the system can effectively manage faults and prevent unsafe states.
This equation sets a benchmark in terms of fault management and the development of comprehensive automotive safety systems. The inclusion of a safety margin beyond mere detection and reaction accounts for delays, system checks, and unexpected operational scenarios to ensure fault mitigation without hazards. This method is crucial for giving the system enough time to deal with faults safely, not just react quickly.
While ISO26262 provides a framework for automotive functional safety, understanding concepts such as Malfunctioning Behavior Manifestation Time (MBMT) and Hazard Manifestation Time (HMT) offers a deeper insight into the timing and behavior of faults and hazards in ensuring functional safety. The kVA article, FTTI at the Concept Level, is an excellent reference that effectively illustrates these concepts, helping engineers design more reliable and safer automotive systems.
MBMT is the time it takes for a fault to manifest itself as a noticeable malfunctioning behavior in the system. This interval starts from the moment a fault occurs and ends when the fault leads to a behavior that can be detected as irregular. The length of the MBMT can vary significantly based on the type of fault and the system’s design. For example, a fault in a sensor might manifest more quickly than one in a software algorithm due to differences in processing and response times.
Understanding MBMT is essential for designing effective diagnostic and monitoring systems. By knowing how long it typically takes for a fault to manifest, engineers can ensure that diagnostic mechanisms are capable of detecting any faults within that timeframe.
HMT measures the time from the onset of malfunctioning behavior to the point where a safety goal is compromised. Unlike MBMT, which relies heavily on system design, HMT is more influenced by operational conditions and the severity of the malfunction. It assesses the urgency of safety measures needed to prevent potential hazards from becoming unsafe conditions.
HMT’s sensitivity to operational scenarios and the seriousness of the malfunctioning behavior takes into account factors such as vehicle speed, environmental conditions, and driver interactions, which can play significant roles in how quickly malfunctioning behavior can escalate into hazardous events.
By understanding MBMT and HMT, engineers can design diagnostic and response systems that operate within these critical time intervals and ensure that faults are detected and addressed before they can lead to hazardous events. Moreover, incorporating MBMT and HMT into safety analyses provides a more detailed understanding of the timing aspects of fault detection and response, enhancing the thoroughness of safety mechanisms.
Looking forward, the integration of FTTI into automotive safety design will continue to refine safety margins and tolerances against real-world uncertainties. This approach ensures safety systems maintain resilience beyond ideal conditions, effectively managing faults, and preventing unsafe outcomes. By adhering to ISO 26262 standards and leveraging insights from concepts such as MBMT and HMT, engineers can enhance the reliability and responsiveness of automotive safety systems, ultimately advancing safety across diverse driving environments and scenarios.
Other Articles
Learn why empowering employees alone doesn’t guarantee success. Discover how strategic alignment and leadership support drive real results.
Generative AI tools like ChatGPT are revolutionizing software engineering by converting UML diagrams into accurate, structured code. Learn more about it here.
AI-powered requirement review tools simplify engineering verification, ensuring accuracy, efficiency, and compliance with INCOSE guidelines. Learn more about it here.
Managing and optimizing thread overhead is important for safety-critical and embedded systems. Learn more about the C++ multithread common myths here.
Managing and optimizing thread overhead is important for safety-critical and embedded systems. Learn more about the C++ multithread common myths here.
Discover the critical role of effective interface management in complex systems. Learn how centralized tools, AI-powered solutions, and well-defined processes can prevent errors, enhance collaboration, and ensure safety in industries like automotive and aerospace.
The system requirements analysis process under ASPICE and ISO26262 frameworks shapes automotive system architecture design for enhanced safety, reliability, and compliance. Learn more about it here.
Compliance with ASPICE and ISO26262 standards provides a significant impact on automotive software development. Learn more about it here.
AI technologies like ChatGPT-4 are revolutionizing requirements engineering by improving accuracy, consistency, and efficiency. Learn about the role of AI in refining, validating, and managing project requirements here.
Model-Based Systems Engineering (MBSE) offers a robust framework to streamline the entire engineering process, from design to validation. Learn more about it here.
Data-Oriented Design (DOD) can revolutionize automotive software development by enhancing performance, reducing costs, and minimizing hardware requirements. Learn more about it here.
While ISO 26262 primarily addresses functional safety, SOTIF extends the scope to focus on potential hazards arising from system behaviour, even when the system functions as intended. Learn more about it here.
Discover the risks of reinterpret_cast in safety-critical software and explore safe alternatives like polymorphism and templates for robust, efficient code.
In a rapidly evolving technological landscape, the demand for systems that can not only withstand errors but also adapt to them is paramount. This article delves into the world of Fault-Tolerant (FT) systems, emphasizing their significance in maintaining the functionality and safety of critical operations across various sectors. It explores the latest advancements in FT technology, underscoring the importance of resilience and adaptability in ensuring uninterrupted service and safeguarding against potential failures.
In a rapidly evolving technological landscape, the demand for systems that can not only withstand errors but also adapt to them is paramount. This article delves into the world of Fault-Tolerant (FT) systems, emphasizing their significance in maintaining the functionality and safety of critical operations across various sectors. It explores the latest advancements in FT technology, underscoring the importance of resilience and adaptability in ensuring uninterrupted service and safeguarding against potential failures.
Discover the transformative impact of Software-Defined Networking (SDN) and Multicast Addressing on automotive embedded systems. Explore how these technologies enhance communication efficiency, safety, and performance in the automotive industry, leading to cost-effective, scalable, and eco-friendly solutions. Dive into the technical advantages and practical applications for modern vehicles and infrastructure.
Discover how ChatGPT revolutionizes engineering with AI, accelerating learning, enhancing safety, and boosting productivity.
Defect Escape Reduction Rate and feedback loop elevate testing. Learn more about them here.
ASPICE and ISO26262 frameworks improve system development in the automotive industry, ensuring safety, compliance, and high-quality standards.
Conducting software FMEA, FTA, and compliance with ISO 26262 helps developers create software that meets stringent safety requirements. Learn more about it here.
Explore the challenges of dynamic memory allocation in critical software, learn how to mitigate failures, and ensure the reliability of safety-critical systems. Real-life failures and practical solutions are discussed.
Strong types are a key concept in C++ programming for functional safety. Learn how strong types can reduce errors in critical systems with C++.
Unit testing is an essential part of the software development process. Learn more about it here.
Learn about categorizing requirements, including functional, non-functional, performance, interface etc for effective system management and development.